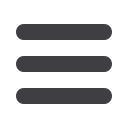
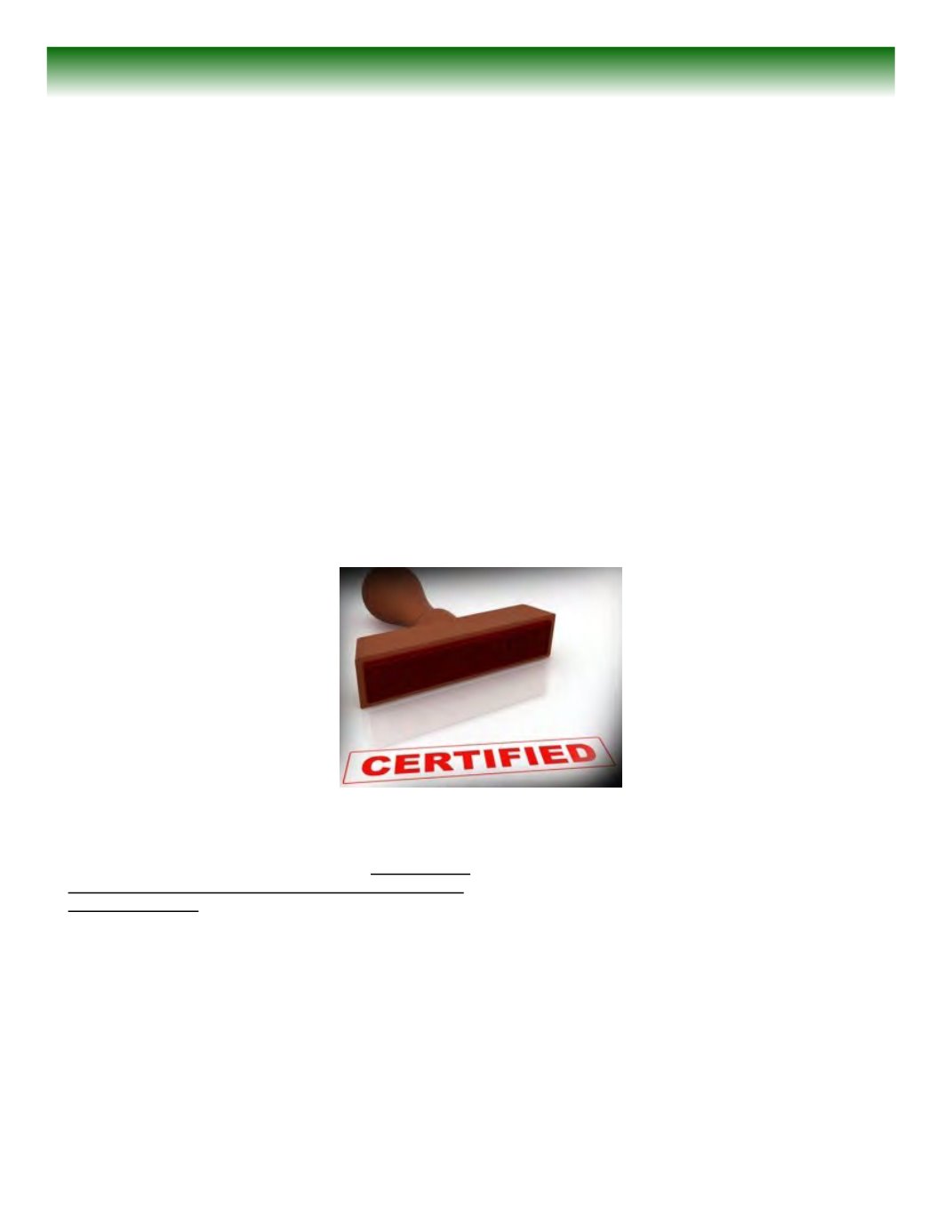
Benefits of Certification to the Customer
In today’s competitive business environment, effective
management systems are indispensable. Customers
want to be confident that they are doing business with
an organization that can deliver quality parts in a time-
ly manner and that meet the legal obligations of the
industry. No customer wants to find out they do busi-
ness with a shop that is one agency visit away from
being indicted. In automotive recycling these man-
agement system are defined through certification
programs.
A certification system promotes and facilitates con-
sistency and improvements in a process or product. It
improves operational efficiency.
Facilities that have
achieved certification communicate to the market
that they have successfully undergone a compre-
hensive assessment and their
process and organization meet
defined standards.
An industry
specific certification program may
not follow the ISO
or International
Organization for Standardization
criteria but it is founded on the
same principles.
ISO 14000 is a family of standards
related to
environmental man-
agement
that exists to help organi-
zations minimize how their pro-
cesses negatively affect the environment, comply with
applicable environmental laws and regulations, and
continually improve. ISO 14001 is similar to ISO
9001
quality management
in that both pertain to the
process of how a product is produced, rather than to
the product itself. Certification is performed by a third-
party auditor. Currently there is no ISO standard for
safety management
but industry accepted BS
OHSAS 18001,
Occupational Health and Safety
Management Systems Requirements,
is an interna-
tionally applied British Standard for occupational
health and safety management systems. It exists to
help all kinds of organizations put in place sound oc-
cupational health and safety performance. ISO
45001 is an as yet unpublished Occupational Health
and Safety Management Standard, set to re-
place OHSAS 18001.
Auto recycling certification programs are patterned
after environmental, safety and, to some degree,
quality management systems. The
value
of using a
recognized management system as a platform for cer-
tification programs is that customers from outside of
the auto recycling industry will understand the signifi-
cance of the certification. The
purpose
of a certifica-
tion system is to instill a cycle of continuous improve-
ment at the certified facility. System may follow the
well-known the Plan-Do-Check-Act cycle.
Plan: set the standards.
Environmental certifica-
tion standards are based on the regulations that gov-
ern the industry and a gap analysis of the member-
ship’s processes to determine areas of improvement.
These "environmental aspects" assists the certifica-
tion program in establishing environmental objectives
or standards. The standards, which
should ideally be measurable,
serve to identify relevant legal re-
quirements.
Do: implement the standards.
Using the information in the certifi-
cation program, the auto recycling
facility implements the changes to
meet the standards. Often these
changes are identified in the initial
on-site audit process.
Check: measure the processes
against the standard.
During the
on-site third-party or self-audit assessment, the facility
identifies processes that do not meet the certification
standard and grades the processes that do.
Act: take action to improve.
After identifying defi-
ciencies in meeting the certification standard, the fa-
cility takes action and makes the changes recom-
mended to meet the standard.
Continual Improvement Process.
These recom-
mendations are incorporated through a continual im-
provement cycle into the facility’s operation and into
the certification program based on changes in the law,
advancement in technology and improved industry
standards.
Environmental management systems are meant to
prevent pollution through accidently release and
maintain compliance. Safety management systems
prevent accidents while maintaining compliance too.
Page 8
Recyclers News Press